Summary
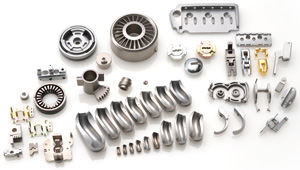
In recent years, diverse processing technologies and methods, such as machining, precision (lost-wax) casting, die casting, press sintering, are being selected and adopted for the forming of metal parts to meet functional and cost requirements. METAMOLD, a metal injection molding (MIM) process, developed as a new 5th generation processing technology in addition to these processing technologies based on our long cultivated metallurgy technology, enables the production of very complex shaped parts similar to plastic products or die cast products, but with savings in resources and energy.
*METAMOLD is a registered trademark of NPR for its Metal injection molding (MIM) parts.
METAMOLD Process
1.Kneading
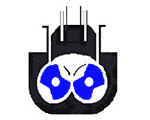
Metal powder and binder (wax + resins, etc.) are kneaded together uniformly.
2.Pelletizing
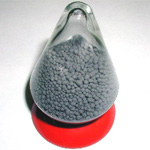
The mixture is pelletized for better moldability.
3.Injection molding
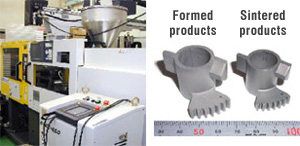
Injection molding is done to produce formed items, similar to plastic products.
- Mold
- The mold will shrink about 10% to 20% after sintering. A mold will be created slightly larger in dimensions than the actual product, taking shrinkage into consideration.
4.Binder removal (degreasing furnace)
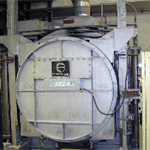
The product is heated to remove the binder.
5.Sintering (continuous sintering furnace)
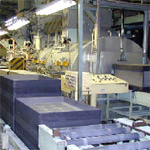
By sintering, a high density sintered product with relative density of 95% or higher is obtained.
6.Inspection / Shipment
Apply post processing (heat treatment, plating, etc.) as required, and pack and ship after inspection.
Features of METAMOLD
1.Costs reduced by forming of complex shaped items integrally.
METAMOLD has enabled the mass production of complex shaped products, similar to plastic and die cast products, from various metals. By enabling integral forming, it has enabled the manufacture of complex shaped parts for all fields at low cost.
2.Enables highly flexible design focused on design and functionality
3.Excellent properties, such as high density and high strength promised
METAMOLD enables the manufacture of sintered items with a relative density of 95% or higher by using very fine metal powder. It has excellent mechanical properties, corrosion resistance and magnetic characteristics, and can provide a maximum surface roughness of around 6S after sintering.
Structural comparison of METAMOLD and conventional powder metallurgical products
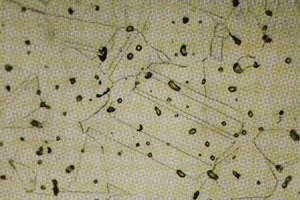
- METAMOLD
- It has excellent mechanical properties for its high density, with vacancies that are spherical and independent.
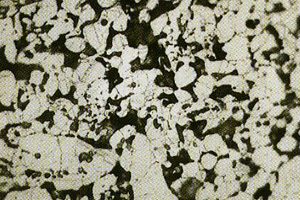
- Powder metallurgical products
- It has poor mechanical properties from its low density, with irregular vacancies existing along the grain boundary.
4.Shows superb dimensional accuracy
Internal stress and powder packing density are uniform because they are formed by introducing metal powder into the metal die cavity using binders. As a result, isotropic contraction occurs and high-accuracy dimension (±0.5% or less) can be obtained.
5.Diverse processing possible
Diverse processing to respond to complicating client needs, such as tapping, mechanical processing like various grinding, quenching and tempering, vacuum heat-treatment, plating, and lubricant processing, is possible.
Material characteristics and applications
Material | Material quality | Characteristics | Applications |
---|---|---|---|
Low alloy steel | Fe-Ni-C | High strength, high toughness | Automobiles, sewing machines, guns |
Fe-Cr-C | High strength, friction resistance | Power tools, hydraulic machinery, musical instruments | |
SNCM,SCM | Shock resistance | Keys, automobiles | |
Stainless steel | SUS316L | Corrosion resistance | Fishing goods, OA equipment, timepieces |
SUS630 | High strength, corrosion resistance | OA equipment, medical parts | |
SUS410L | Electromagnetic characteristics | Electromagnetic parts, valves | |
SUS444 | Electromagnetic characteristics | Electromagnetic parts, valves | |
SUS440 | high strength | Time pieces, medical parts | |
SUS262 | Allergy resistance, high strength | Timepieces, hair dressing | |
SUS420J | High strength, corrosion resistance | Pneumatic machinery | |
SUS440C | friction resistance,corrosion resistance | Spinning machines, blades | |
Titanium | Pure Ti, Ti alloy | Corrosion resistance, light weight | Timepieces, hair dressing |
Other | Super invar | Low thermal expansion | AV equipment |
Kovar | Thermal expansion close to glass | Measuring equipment | |
Cemented carbide | High hardness, high corrosion resistance | Keys, timepieces | |
Heavy alloy | High specific gravity | Weight |
Mechanical properties
Material | Material quality |
Tensile strength (MPa) |
Elongation (%) |
Hardness, etc. |
---|---|---|---|---|
Low alloy steel |
Fe-Ni-C | 1000-1800 | 2 - 10 | HRC 30-50 |
Fe-Cr-C | 1000-1800 | 1 - 7 | HRC 30-60 | |
SNCM | 1120 | 3 | Surface hardness Hv 650 - 700 |
|
Stainless steel | SUS316L | 530 | 40 | |
SUS630 | 1300 | 10 | Post aging process HRC42 |
|
SUS410L | 380 | 45 | ||
SUS444 | 450 | 35 | ||
SUSXM27 | 570 | 25 | ||
SUS420J | 1000 | 8 | HRC ≥40 | |
SUS440C | − | − | HRC ≥50 | |
Titanium | Pure Ti | 555 | 15 | Hv 150-240 |
Ti alloy | 780 | 5 | Hv 260 | |
Other | Kovar | 540 | 30 | |
Cemented carbide | − | − | Hv 1600-1800 | |
Heavy alloy | − | − | Specific gravity 18 |
Design points
Nominal dimensions (mm) |
General tolerance(±mm) | Special tolerance(±mm) | |
---|---|---|---|
Dimensional tolerance |
≤10 | 0.10 | 0.03 |
10<L≤20 | 0.15 | 0.10 | |
20<L≤30 | 0.20 | 0.15 | |
30<L≤50 | 0.30 | 0.20 | |
50<L | 0.5% | 0.4% | |
Angle |
General tolerance(±') | Special tolerance(±') | |
0.5' | 0.3' | ||
Surface roughness |
Rmax | <12S | About 6S |
Injector mark |
0.05 - 0.1mm | ||
Parting line |
0.05 - 0.1mm |
*The values vary depending on material and shape.